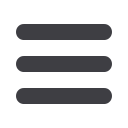
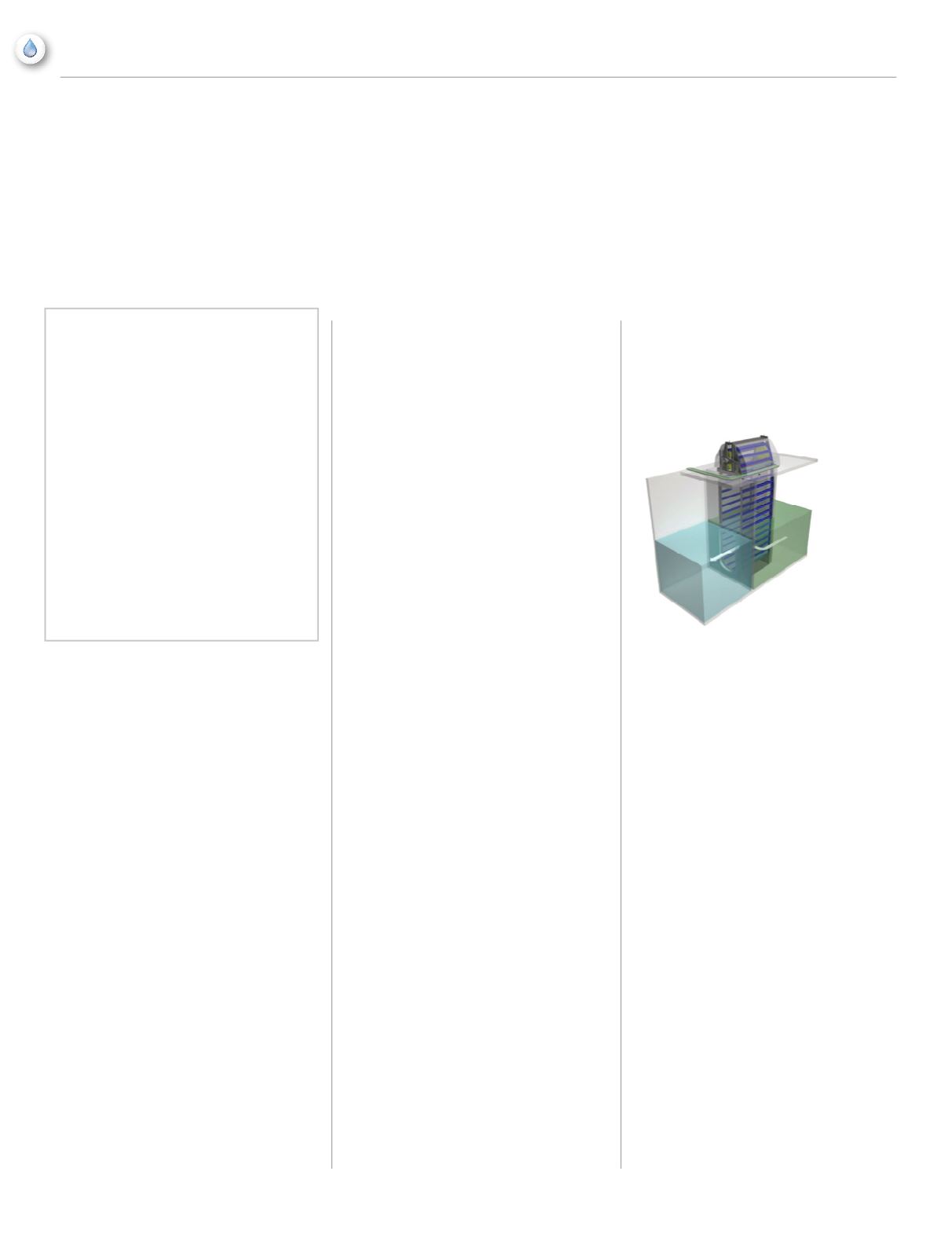
feature
T
ABSTRACT:
This article will review the
properties and selection criteria for
dynamic seals in wastewater applications.
The impacts of the inherent compromise
between sealing ability and seal life will
be reviewed along with the materials,
processes and options that may
affect seal mechanics and application
engineering. This article will contain a
chart of materials and properties; photos
of seal failure impacts; and a review of
potential dynamic seal failure-modes
relative to screening and membrane
protection. Recommendations relative to
seal selection, sealing process strategies
and other options will be included.
he most common modes of seal failure are by
fatigue-like surface embrittlement, abrasive
removal of material, flex-cracking and
corrosion.Abrasive particles in the wastewater
stream have a strong influence on the wear
resistance of seals, the wear rate of the seal
increasing with the quantity of environmental
contamination. A good understanding of the
wear mechanism involved will help determine
potential seal deterioration. Contaminants
from the environment such as sand can
become embedded in the seals causing
abrasive cutting. Elastomer wear is analogous
to metal degradation.
As the use of specialized membranes in the
wastewater industry to meet more stringent
standards and to support the trend toward
direct reuse increases, the reliability of
dynamic seals in pre-screening technologies
becomes more critical. This brings the focus
to dynamic seals as the weakest link in the
protection of downstream processes. For this
reason, the specification of the appropriate
seal material for each application and sealing
strategies becomes imperative. This is
because seal failure is progressive and can go
undetected until it becomes catastrophic to
high-value downsteam technologies.
Process Protection—an Essential
Membrane technology is increasingly central
to wastewater processing. This trend can be
expected to grow with the expanding focus on
the reuse of wastewater. However, membrane
technology is especially vulnerable to
oversized debris within the waste stream. This
vulnerability in turn places a special emphasis
on the reliability of prescreening technology.
In many cases, this critical prescreening step
is performed by band-type screens, which
rotate perforated metal panels in front of
the process flow to capture oversized debris.
To accomplish the movement of the metal
panels—which is necessary for the removal
of debris—these panels are mechanically
rotated. Seals are used to isolate the front of
the panels (influent-facing) from the back of
the panels (effluent-facing). Seals are also
used to prevent leaks of influent into the
effluent stream at the rotating edge of the
band of assembled panels
(see figure 1)
. At
the rotating edge a lip-seal is used. This seal
is subjected to various type of wear from
abrasion at the surface-to-surface contact as
well as from material (i.e., sand, grit, glass,
etc.) leeched from the debris stream. The
seals between the metal perforated panels are
subjected to a continuous cycle of flexing as
the band of panels rotate for the purpose of
debris removal.
This means that in many cases, the protection
of the downstream membrane(s) depends on
two types of rotating seals—specifically seals
that can abrade and fail (at the rotating edge)
as well as seals that can fatigue, elongate and
fail (between the individual perforated metal
panels). For this reason, a careful compromise
has to be made between a variety of wear
factors. These factors include: the elasticity of
the seal, the hardness of the seal, the tensile
strength of the seal as well as several other
basic seal properties.
About Seal Properties
Seals for use in rotating assemblies (aka,
dynamic seals) are available in a spectrum
of materials with specific properties. Some
are harder and longer lasting, but sacrifice
flexibility and resiliency to achieve this
goal. Others are resistant to swelling
and degradation from chemical agents at
the expense of elasticity. This inherent
compromise in seal properties make seal
selection a challenging compromise. (
See
Seal Material Overview and Chart A
)
Tests conducted at Massachusetts Institute of
Technology (MIT) show that the seal wear
process occurs in two stages: the break-in
period and the aggressive wear period. During
the break-in period the seal does not wear.
During the aggressive wear period, however,
particles under the contact band cluster and
form an abrasive front that erodes the seal lip
at a rapid rate.
In the seal-wear example shown below,
(see
figure 2)
, the penetration of particles into
the contact band of the seal as a function of
By Mike Pruitt, Duperon
20
NCRWA.COM|
Winter 2015
DYNAMIC SEALS
THE “SEALING ABILITY VERSUS SEAL LIFE” COMPROMISE
MATERIALS, PROCESSES, OPTIONS
Figure 1:
Typical band-type
perforated screen.