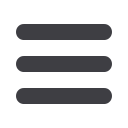
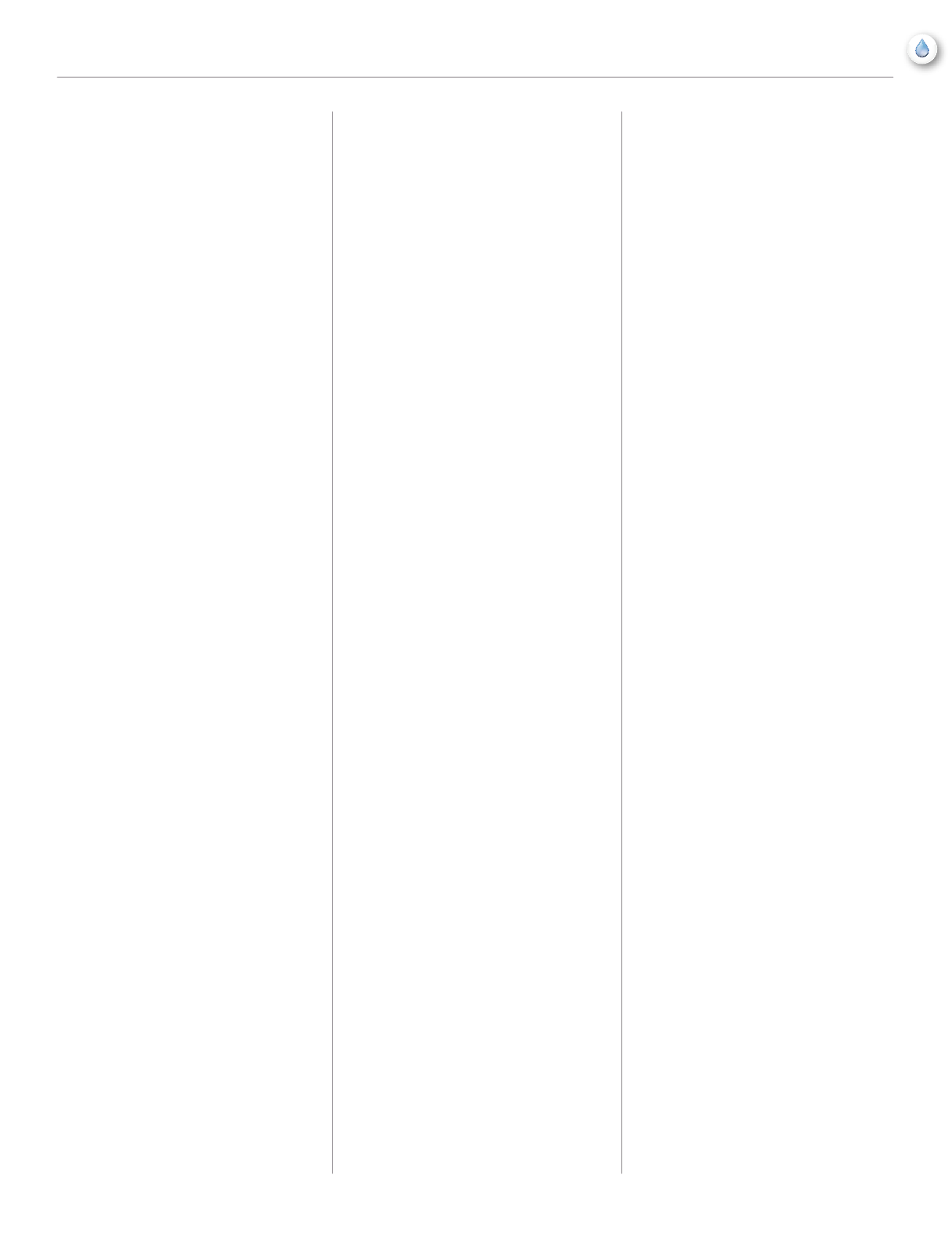
Winter 2015
NCRWA.COM23
feature
substitution of these materials for traditional
thermosetting materials results in such
benefits as significantly increased production
speeds (via conventional plastic injection
molding machines) and the ability to reuse
clean scrap without a loss in physical
properties. This results in a reduced part
cost due to minimized scrap loss. Also,
they are available in a broad range of
durometers and colors and, by adjusting the
percentage of hard (plastic) segments in the
copolymer matrix, the physical properties
can be modified. For example, as styrene
content is increased in polystyrene elastomer
block copolymers, they change from weak
rubber-like materials to strong elastomers, to
leathery materials, to finally hard, glass-like
products (with styrene content above 75%).
Limitations:
The physical properties of
thermoplastic elastomers are highly
dependent upon the properties of the
plastic and elastomeric regions of the
copolymer. Consequently, as temperature
changes, so does the behavior of the TPE.
The low temperature limit is defined by
the glass transition temperature of the
rubber phase, below which the material
is brittle. Likewise, the high temperature
limit is defined by the melting point of the
plastic phase, above which the material
softens and begins to flow. This results in
lowering the overall heat resistance of the
copolymer. Also, as temperature increases,
compression set increases which limits the
overall component size and complexity
due to stack-up tolerances. Likewise, the
chemical resistance of the thermoplastic is
determined by the limits of BOTH materials
comprising the system.
Important Seal
Related Definitions
2
Compression Set
Elastic recovery is a measure of the
elastomer’s ability to return to its original
shape once a compressive force has been
removed. Failure of the seal to return to
its original shape after compression is the
condition termed “compression set” and all
seals exhibit some degree of compression set.
Determination of the amount of compression
set is governed by ASTM designation D395
test procedure.
Tensile Strength
Tensile strength is an indication of how
strong a compound is. Any time you have an
application where you are pulling on the part,
tensile strength is important to know. Whether
a product is designed to break easily or not at
all the tensile strength defines how the object
will react to the tensional forces. A few rubber
products where tensile strength is important
would be bungee cords, rubber tie downs,
drive belts. Some elastomeric compounds,
like Silicone, have a low tensile strength
making them unsuitable for dynamic type
seals because they can fracture easily.
Tear Resistance
The tearing of rubber is a mechanical
rupture process started where forces are
concentrated in an area usually caused by a
cut, defect or deformation.
Abrasion Resistance
This term is used to indicate the wear
resistance of a compound. It is concerned with
scraping or rubbing of the surface and must
therefore always be considered for dynamic
seals. Compounds of medium hardness (about
70 durometer) are usually more resistant to
abrasion than harder or softer compounds.
Resilience
Good resilience is an important attribute in
a moving seal. Resilience in most cases is
dependent on proper compounding techniques.
Of the base polymers, however, natural
silicone and rubber have the best resilience.
Original resilience of a compound is not the
whole story, as resistance to compression set
is very important in prolonged service.
Elongation
This property determines how much a seal
can safely be stretched during installation. It
is expressed as a percentage increase over the
initial length of the seal. Ultimate elongation
is the percentage of stretch at the time the seal
breaks. The smaller the diameter of the seal,
the more important its elongation properties,
especially when the seal must be stretched for
installation. Combined with tensile strength
measurements, elongation also describes
the compound’s ability to recover from peak
overload, or from force localized in one
area of the seal. If the elongation changes
significantly after exposure to a fluid, that is
a clear signal that the compound is degraded.
Durometer to Modulus
Durometer is an indirect measure of the
stiffness, or more correctly the modulus, of
an elastomeric material. Modulus, in turn, is
a property of elastomers, analogous to the
same property of metals, which is the ratio
of stress to strain in the elastomer at some
loading condition (i.e. the slope of the stress-
strain curve). Unlike metals which typically
have a linear stress-strain curve below their
yield point, the stress-strain relationship of
elastomers is non-linear over a range of loading
conditions and can be significantly influenced
by ambient temperature. As a result, the
modulus of an elastomer is highly dependent
on the conditions under which it is measured.
In a relative sense, low durometer or hardness
correlates to a low modulus or stiffness.
Similarly, as durometer increases so does
modulus and vice-versa. However, the
correlation between durometer and modulus
is not directly proportional, i.e. a doubling in
durometer value does not equate to a doubling
in modulus.
About the Author:
Mike Pruitt is the Director
of Marketing for Duperon Corporation
and is a 30-year water and wastewater
industry veteran. Mike can be reached
at
mpruitt@duperon.com.
Neoprene
®
and Viton
®
are registered trademark
of DuPont Performance Elastomers.
References:
1
South, Joseph Thomas, Mechanical Properties
and Durability of Natural Rubber Compounds
and Composites. Dissertation. Virginia
Polytechnic Institute, December 14, 2001.
2
Apple Rubber Products, Materials Selection
Guide. Commercial Catalog, 2015.
3
McGrosky, Dale T, Physical Properties of
Rubber. Satori Seal Corporation article, 2015.
4
Matthews, Robert and Freerks, Fred, The
Right Seal. Green, Tweed & Company
handbook, 2015.
Ayala, H.A., Hart, D.P.,Yeh O., and Boyce,
M.C. Wear of Elastomeric Seals in Abrasive
Slurries. Massachusetts Institute of
Technology study, 1998.