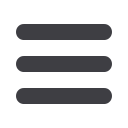
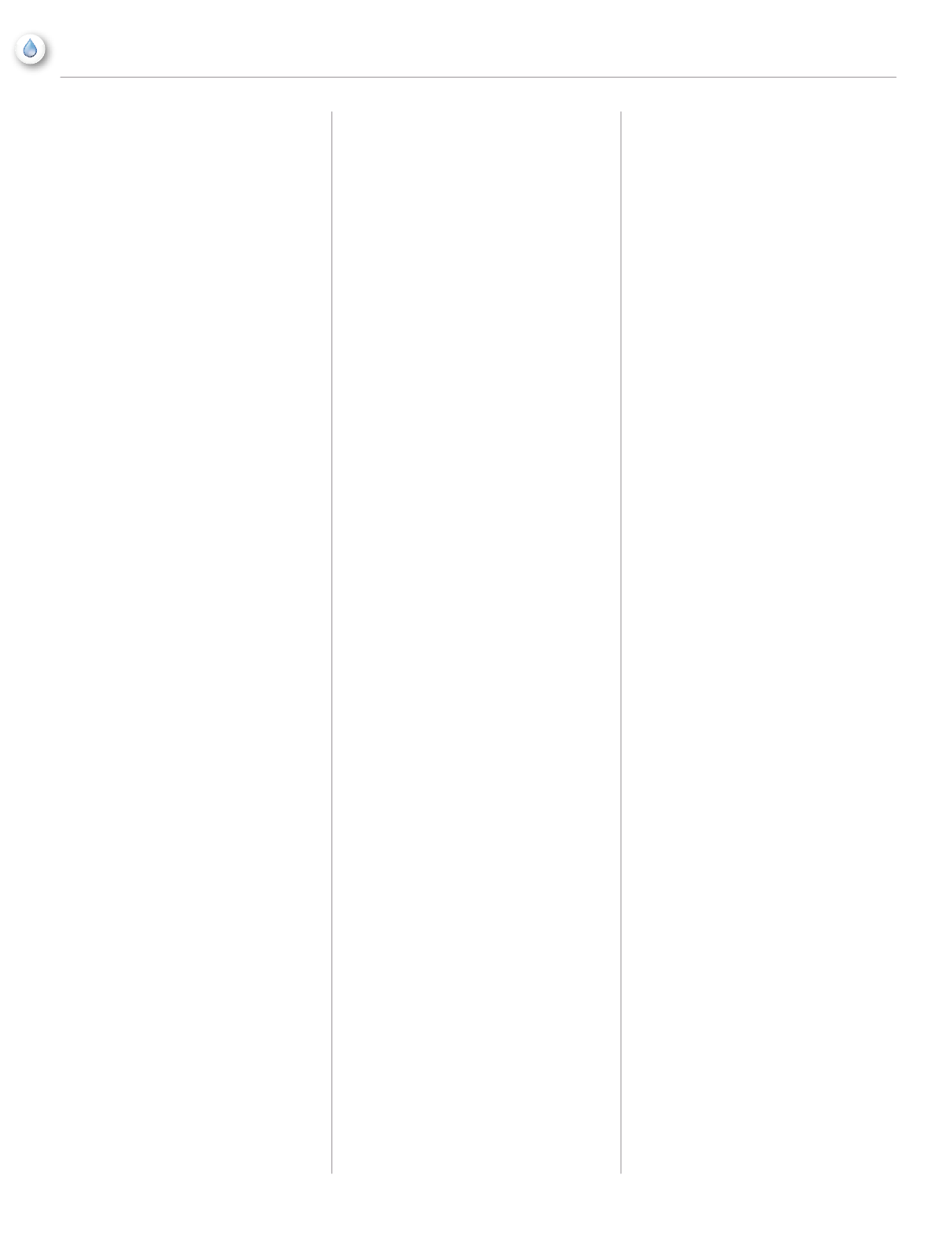
22
NCRWA.COM|
Winter 2015
feature
chlorinated, aromatic and nitro hydrocarbons.
Because Nitrile is economically competitive
with Neoprene, and generally has superior
performance characteristics in most situations,
it has largely replaced Neoprene
®
in the
O-rings of today.
Nitrile (Buna-N):
Features:
Comprised of the copolymer
butadiene and acrylonitrile, in varying
proportions. Use of Carboxylated Nitrile can
have superior abrasion resistance, while still
having improved oil resistance.
Limitations:
Nitrile compounds are attacked
by small amounts of Ozone. Phthalate
type plasticizers are commonly used in
compounding Nitrile rubber. These plasticizers
can migrate out and cause problems with
certain plastics. Also, new regulation on
certain phthalates have limited their use.
Nitrile (Hydroginated):
Features:
Like Nitrile, increasing acrylonitrile
content improves oil resistance at a cost of
reduced low temperature performance.
Limitations:
Like Nitrile, HNBR is not
recommended for exposure to ethers, esters,
ketones, or chlorinated hydrocarbons.
Polyacrylate:
Features:
With excellent resistance to hot
oil, automatic transmission and Type A
power steering fluids, the greatest use
for Polyacrylate is found in automobile
manufacturing, where O-rings of this
material are employed to seal components of
automatic transmission and power steering
systems. Highly resistant to sunlight and
ozone degradation, Polyacrylate also features
an enhanced ability to resist flex cracking.
Limitations:
While resistance to hot air aging
is superior to Nitrile, Polyacrylate strength,
compression set, water resistance properties
and low temperature capabilities are inferior
to many other polymers. Polyacrylates are
also not generally recommended for exposure
to alcohol, glycols, alkalis, brake fluids, or to
chlorinated or aromatic hydrocarbons.
Fluorosilicon:
Features:
Fluorosilicone is most often used in
aerospace applications for systems requiring
fuel and/or diester-based lubricant resistance
up to 400°F. Although generally specified
for aerospace use, due to its excellent fuel
resistance and high temperature stability,
Fluorosilicone is becoming an increasingly
popular material for a wider range of sealing
applications. Featuring good compression
set and resilience properties, fluorosilicone
compounds are suitable for exposure to
air, sunlight, ozone, chlorinated and
aromatic hydrocarbons.
Limitations:
Due to limited physical strength,
poor abrasion resistance, and high friction
characteristics, Fluorosilicone elastomers
are not generally recommended for dynamic
sealing. They are predominately designed
for static sealing use. They are also not
recommended for exposure to brake fluids,
hydrazine, or ketones.
Fluorocarbon:
Features:
High fluorine grades offer higher
resistance to swell in high octane and
oxygenated fuel blends. This gives superior
performance in Ethanol/Methanol blended
gasoline. Base resistant grades offer
improved resistance to amine based oil
protectants found in new transmission oils.
Also, improved resistant to steam for higher
temperature services. Low temperature
bases can improve performance to -40°F.
New polymers being offered have improved
chemical resistance and low temperature
performance. Viton
®
Extreme™ ETP
offers similar chemical compatibility as
Kalrez™ with temperature resistance to
+446°F. Special compounds, using new
polymer technologies, provide improved low
temperature performance with a TR(10) of
-40°F and brittleness to -76°F.
Limitations:
Fluorocarbons are not
recommended for exposure to ketones,
amines, low molecular weight esters and
ethers, nitro hydrocarbons, hot hydrofluoric
or chlorosulfonic acids, or Skydrol
®
fluids.
They are also not recommended for situations
requiring good low temperature flexibility.
Silicon Rubber:
Features:
When properly prepared, possible
benefits include fulfillment of USP
Class VI and ISO 10993 requirements,
embrittlement from gamma sterilization,
sterilizable with EtO/steam. Also, this
grade of silicone is generally transparent
due to class requirements.
Limitations:
Generally, low abrasion and tear
resistance, and high friction characteristics
preclude silicones from effectively sealing
some dynamic applications. Silicones are also
highly permeable to gases and are generally
not recommended for exposure to ketones
(MEK, acetone) or concentrated acids.
Butyl Rubber:
Features:
With outstanding low permeability to
gases, Butyl is especially effective in vacuum
sealing applications. It also features good-
to-excellent resistance to ozone and sunlight
aging. Butyl further features excellent shock
dampening capabilities. Only slightly affected
by oxygenated solvents and other polar liquids,
Butyl is often utilized in seals for hydraulic
systems using synthetic fluids. It is good with
MEK, and silicone fluids and greases.
Limitations:
Because it is a petroleum product,
Butyl has poor resistance to hydrocarbon
solvents and oils, and diester-based
lubricants. Halogenated butyl has been
introduced to expand oil and chemical
resistance to this polymer. Chlorobutyl and
Bromobutyl have better resistance.
Polyurethane:
Features:
Polyurethane offers superior seal
performance in hydraulic situations, where
high pressures, shock loads, or abrasive
contamination is anticipated. Polyurethane
possesses chemical compatibility similar
to that of Nitrile, offering good resistance
to petroleum-based oils, hydrocarbon fuels
and hydraulic fluids, the oxidizing effects of
ozone, and the aging effects of sunlight. It
also has good tear resistance.
Limitations:
Unless specially compounded, at
elevated temperatures Polyurethane begins
to soften, losing its physical strength and
chemical resistance advantages over other
polymers. Tending to rapidly deteriorate
when exposed to concentrated acids, ketones,
esters, chlorinated and nitro hydrocarbons,
Polyurethanes are also prone to hot water and
steam degradation.
Thermoplastic Elastomers (TPE):
Features:
In virtually all cases, the